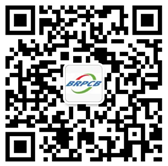
凡从事线路板之业者,莫不饱受孔破问题之困扰,孔破问题几乎成为线路板之顽疾。从制造各工序的管理到O/S测试的拦截,乃至使用造价高昴却效率低下的微阻测试机,各种方法竞相使用,但孔破却依然时隐时现,直至流失到终端客户处,轻者造成客户投诉,重者引发巨额赔款。本文即从孔破的各种形态分析其成因并尝试探索解决方法与大家共享。
一.概述
1定义
孔破指的是在孔壁金属化过程中或完工后,其原本应完好覆盖孔壁的孔铜出现了局部破洞、环状孔破,孔壁裂缝、整孔无铜的现像而称之。
2影响
孔破所造成的影响,轻者于功能测试时经电测测得而报废,造成工厂成本的浪费,严重者则流失到客户端产生PCBA报废。孔破为什么会跳过O/S测试的关卡而流出?一般而言PCB工序中的孔破,并非真正的破断而形成完全OPEN状态,而是藕断丝连的疑似孔破,测试时无法有效侦测出而判为PASS,当作良品而出至客户端,而当客户贴完零件经过两次回焊高温冲击(熔焊温度约220℃)则疑似孔破的孔其孔铜最薄弱的地方就彻底断开了,断开之板即可被ICT功能测试侦测出来,此时线路板便呈现出真正的孔破。
二.常见的孔破类型
1. 基材造成的孔破
a.与CTE因素有关的孔破
b.板材特殊化性造成的孔破
2. 钻孔造成的孔破
a.孔塞导致的孔破
b.孔壁粗糙度过大导致的孔破
c.钻孔断针导致的孔破
d.钻孔孔偏导致的孔破
3. 电镀造成的孔破
a.PTH孔破
b.一铜不良导致的孔破
c.镀锡不良导致的孔破
4. 干膜造成的孔破
a.正片流程干膜盖孔不良导致的孔破
b.干膜膜屑残留孔边造成的孔破
5. OSP/化银/化金等药水残留导致的孔破
6. 喷锡热应力造成的孔破
三.孔破分析
1基材造成的孔破
1.与CTE有关的孔破
随着无铅时代的到来,板材本身之耐热性也需随之提高,故选择合适的板材方可避免先天之不良。早期的PCB板材绝大多数是普通Tg的FR-4板料,与有铅焊锡组装搭配尚可应付,而应对现在的无铅焊接, 普通Tg的FR-4板料已有些力不从心了。随着科技的进步与无铅焊接的要求,中Tg,高Tg,无卤素等板材也应运而生,而CTE值的匹配性更不可忽视。因不同的板材其CTE会有所不同,而基材的CTE又大于铜(一般而言,基材:铜=12:1),一旦两种材料热膨胀系数相差过大,在高温的条件下就可能发生孔铜拉裂(Crack),即孔破现象。如下图所示,是因CTE因素造成的孔破。
注:CTE-COEFFICIENT OF THERMAL EXPANSION(热膨胀系数)
2.板材特殊化性导致的孔破
特殊的板材(如陶瓷板、Teflon),因化学性质迟钝造成孔壁极难活化。下图孔破所用为陶瓷板使用传统的化学铜制程做沉铜,经过多达三次PTH后孔壁依然没有沉积上铜,孔破发生的概率相对普通板材要高出很多。故特殊的板材需考虑到孔壁粗化的程度是否足够,或使用特殊流程方能进行镀通孔制程。
2钻孔造成的孔破
1.孔塞型孔破
下述图片为钻孔产生的粉屑,可能是钻机吸尘力不足导致孔内粉屑残留,在电镀前处理时无法去除干净。而粉屑本身对化学铜的附着是没有任何影响的,一旦化铜上去,一二铜随即呈包裹式沉积,形成包夹式坚硬的铜粒于孔中,而在粉屑与孔壁的界面药水则很难渗透,故化学反应在这里也就无法进行,孔塞型孔破也就随之产生。此类孔破较易辨识,切片后在显微镜的背景下,外面包裹的铜呈现金属光泽,而钻孔粉屑则因不反光而呈现黑色的特征。
2.钻孔孔壁粗糙度过大孔破
一般情况下,孔壁粗糙度过大是由于钻针缺口或者是钻针变钝导致,钻针有缺口时则在钻孔过程中钻针刃面无法对孔壁进行一致性整齐切削,缺口部位对孔壁进行撕扯式切削,使得孔壁出现粗糙度过大,甚至形成凹坑(如红色箭头处)。而当钻针刀刃变钝时,则在切削孔壁时无法产生一刀两断式的切削效果,而是拉断式切削,除了孔壁粗糙度变大,还会伴随出现钉头现象。这种情况下孔壁在PTH化铜时落差大的地方容易残留气体,阻碍沉铜,即使在摆动,振动,气动,打气等辅助装共同协作下,也无济于事,化铜无法立足,一铜也无从谈起,孔破就产生了。
3. 孔内断针造成的孔破
钻针断在孔内基本是无法处理的,即使取出来,板子也基本报废了。一般断针主要与其本身的材质,研次等有关。当然与钻孔参数也有关系,如迭板的片数、进回/刀速、铝片的皱褶等等,这些因素也会造成断针。孔内断针造成的孔破,不足畏惧,因为孔内断针完全封死药水信道,断针位置不可能上铜,是完完全全的OPEN,在后面的测试中完全可拦截,较少有流失至客户端,同时现在的钻机基本上都有断针侦测功能,故在钻孔阶段就能识别出来,完全可做到早发现,早防止。
4.激光钻孔偏位造成的孔破
众所周知,单孔偏位(飞孔)是钻孔所致。钻孔造成的偏移度在2mil内允收,偏移度过大会造成孔破,此类孔破主要发生在正片流程(TENTING)。钻孔偏位超过2MIL,干膜对偏超过2MIL,二者累加,则干膜不能完全盖孔,在DES工序,蚀刻药水可进入孔内,将孔铜咬蚀,孔破即会发生。
下面切片图为雷射(laser)盲孔偏移所造成的孔破,在HDI的流程中,其精准度更为重要,一旦偏移即产生孔破。HDI板通常采用正片流程生产(因为在肓孔内镀铜尚且有难度,一般铜厚度约600U”,再镀锡作为抗蚀阻剂,则更难了,所以选择正片流程),盲孔及PAD由干膜覆盖,一旦孔位不正,破出PAD,则干膜无法完全盖住孔,蚀刻时药水侵入盲孔咬蚀铜造成孔破。
3电镀造成的孔破
1.PTH孔破
⑴.气泡造成的孔破
在电镀工序,孔破的类型很多,一般在沉铜过程中最常见的是孔内气泡未赶出造成的孔破。此类孔破的位置一般在孔中央,孔破位置呈现出二铜包一铜的特征(针对孔破不良板在做切片时要进行微蚀,以便清楚看到一铜与二铜的界限,对于判定孔破有重要意义)并且孔破形状多为对称型,断口处之轮廓呈弧形。此孔破之成因,通常是振动,摆动或气动辅助装置效果不佳使得孔内的气泡无法赶出,导致气泡残留孔内,造成有气泡的地方无法沉铜,进而影响电镀铜,从而诱发孔破。
⑵.除胶渣过度造成的孔破
在除胶渣工序,若发生除胶渣过度,则也可能诱发孔破,除胶渣过度一般在切片后基本可以判定,即孔壁出现回蚀现象(内层铜环超出基材位置,且树脂相对玻纤明显有内缩,形成玻纤与树脂部分的高低差)除胶渣过度导致孔壁粗糙度过大,则局部死角位置易出现孔破。另外伴随除胶渣过度出现的现象是孔壁很可能出现灯芯效应。除胶渣是先通过膨松剂的溶胀作用降低树脂分子间之键结能,再利用高锰酸钾的强氧化性去咬蚀树脂,进一步形成孔壁微粗糙的目的(micro-rough),便于化学沉铜。在药水浓度及其它参数受控的前提下,除胶渣过度通常是因为PTH返工经过了二次除胶渣所致,故一般PTH返工是不能走二次除胶渣的(除非特殊化性的板材,例陶瓷板通常是要走两次除胶渣)。
⑶.药水问题造成的孔破
好的孔壁是沉铜好的前提,假设化学药水本身出问题,则孔壁做得再好,也是无济于事。药水问题导致孔破,通常有以下几点:
①去脂平整不良,去脂平整又称清洁或整孔,其最主要的目的是调整孔内电荷。钻孔完工后,孔壁呈现负电性,整孔的作用是将孔壁负电性调整为正电性,然后在活化槽,经活化后,带负电的钯离子团与带正电的孔壁形成“异性相吸”的效果使得钯得以在孔壁吸附,为沉铜准备。而若整孔药水出问题,比例浓度,成份,温度变异,则整孔就会出现不良。
②活化不良,活化的目的是在孔壁吸附钯离子团,为沉铜做准备,若活化药水出问题,同样会诱发孔破。而在沉铜线药水的管理中,活化的管理是非常关键的,本身活化药水是非常昴贵的,一旦发生不良需要换槽解决问题,则只有浪费药水了。而活化药水的管理中,活化剂浓度需要严格管理,尤其是钯浓度,通常用AA仪可以精确分析其浓度,并设置自动添加系统,做到少量多次添加,维持药水浓度稳定。
③沉铜药水不良,沉铜药水管理不当,将直接导致背光不良从而出现孔破。因沉铜是利用化学反应原理而进行的,且化学铜药水有多达五种成份(氯化铜,甲醛,氢氧化钠,安定剂,敖合剂),这五种成份其浓度要严格管制,如此才能保证药水平衡,反应才能正常进行。PCB的整个工序中,唯一需要每两小时分析一次的药水就是沉铜药水,可见其变化之快。故沉铜药水是必须设置药水自动添加系统的。另外就是当停线后重新开线生产时,
必须要用假镀板进行启镀,以提升药水活性,通常启镀板需要5-8槽,各厂家视其自身的需要而定。其次是对沉铜效果的监控,即背光监控,通常背光切片是每一小时一次,且背光等级严格依SOP进行判定,当出现背光不良,不必心存侥幸,要立即查找原因,并对背光不良嫌疑板进行返工。
2.一铜孔破
⑴.气泡造成的孔破
气泡造成的孔破多发生在孔中央,与PTH气泡型孔破有点类似,而且断口位置也是呈现二铜包一铜。与PTH气泡型孔破不同的是,一铜孔破还有其它因素,一铜时若孔内气泡残留,则一铜无法镀上,仅有一点微薄的化学铜远远无法低挡D/F及二铜前处理微蚀的攻击,故而发生孔破。
⑵.铜渣塞孔造成的孔破
因槽液中有金属颗粒悬浮,在搅拌及振动的作用下,金属颗粒卡在孔口,在电流的作用下孔口处的铜越来越厚造成药水无法贯入孔内,孔破也就产生了 。
3.二铜(镀锡)孔破
⑴.镀锡不良(气泡)造成的孔破
关于气泡型孔破,PTH,一铜,二铜都存在,但二铜气泡型孔破与前二者有明显的区别,二铜气泡型孔破通常发生在镀锡过程,其孔破断口处为斜角,因为镀锡时若有气泡在孔内则锡无法镀上,在蚀刻时铜失去保护,蚀刻药水直接攻击铜层,导致孔破,因为药水首先是攻击二铜,再攻击一铜,故断口处类似刀切的痕迹,且二铜未包裹一铜。同时另外一个特征与PTH及一铜相似,即孔破位置左右两边呈对称分布。
⑵.镀锡不良(药水贯孔性不佳)造成的孔破
由下图来看,孔破处的特征为一二铜均存在,孔破位置二铜未包裹一铜,并且由孔口向孔中心呈现渐薄的态势,故判定为锡过薄导致的孔破(镀锡厚度通常要求200—400 MICRO INCH)使得药水咬蚀锡铅下面的孔铜,从而造成了孔破。此类孔破其基本成因是锡药水贯孔性不佳导致小孔中间部位锡厚不足,蚀刻时较薄的锡层不足以保证铜层,使药水慢慢侵蚀,故此类孔破大多呈现自孔口至孔中间渐薄态势,也有称其为沙滩型孔破的。此类孔破另有一个特征是二铜未包裹一铜,但不同于镀锡气泡型孔破,因为此类孔破,其断口处不是呈现刀切之斜面,而是呈现削铅笔式的层次感。
⑶.镀铜延展性不足造成的孔破
从图片可以看出,此类孔破孔壁并没有完全断开,而是出现一种“藕断丝连”的现象,这类孔破若发生在客户端可能会出现过炉后断开,但ICT测试OK,但在终端客户处使用时又断开,因为这类孔破随着温度的升降会出现时而断时而连之现象。造成此种孔破现象是因铜的延展性不佳所致。延展性不佳,则其首要原因来自电镀添加剂问题,众所周知,电镀铜添加剂中之光泽剂主要作用是改善镀铜的致密度,光泽度及铜的结晶,虽然其含量低(0.2—0.8ml/L),但其作用不可轻视.没有光泽剂的铜层其致密度非常差,延展性糟糕,铜的结晶呈现出颗粒大,疏松的特征,遇高温极易出现孔铜断裂。
4. 干膜造成的孔破
1.干膜Tenting孔破
Tenting孔破,只发生在正片流程的产品中,若走正片流程,首先应该考虑该产品最小Ring边宽度,Ring边过小,干膜就会立足不稳从孔边滑落。一般Ring边的安全宽度需在MIN 4MIL以上(干膜附着力在4MIL以上才有最基本的保障),而且还要保证药水的温度,温度过高,干膜变软,一旦药水槽的温度超出干膜所能承受的最高温度,那么破膜发生的机率就大大增加。另外钻孔时飞孔问题及干膜本身的对偏问题都可能导致此类孔破。
2.干膜残存孔边造成的孔破
从图片上可以看出,孔破的位置均在孔口处,并且呈现圆弧状或鹰钩状,且二铜未包裹一铜,另外下端呈现出刀切之斜面,说明药水由外向内攻击铜面。此种现象首先可以判定是走负片流程(若是正片流程应是孔内大面积无铜,且不会局限于孔口位置),且是在干膜后膜屑贴附于孔口位置,导致二铜及锡皆未镀上。从上端的圆弧状可以判断出,二铜顺着膜面延伸,故呈现出一定的弧度。
5. OSP/化银/化金等药水残留导致的孔破。
从图片可以看出孔破的形状呈现不规则现象(锯齿状),且二铜未包裹一铜,同时孔破位置在靠近塞孔油墨位置且铜面有发黑的迹象,故判定是被药水咬蚀造成的。此种孔破是因为塞孔不饱满(孔两端有油墨,中间空洞,或只有一边孔口处有油墨,)在后工序OSP,化银,化金等表面处理时微蚀药水残存孔内无法有效清洗干净,导致药水缓慢攻击铜层,从而导致孔破。特别是化银的表面处理,除了前处理有微蚀的药水有攻击作用之外,再加上化银槽还有硝酸的成份,对铜同样有攻击作用。以上孔破是两种因素共同作用所致,塞孔不良是主因,药水残留是诱因。综上所述,我们不要一提到孔破就立即联想到电镀问题,塞孔不良导致的孔破其严重性并不亚于电镀问题导致的孔破。故如何塞好孔是防焊应该要解决的问题。
6. 喷锡热应力造成的孔破
无铅喷锡对孔铜的考验是非常大的,孔铜稍薄就会被拉开、拉裂;再者就是喷锡本身的条件,若喷锡温度过高,使得板子在瞬间接受较大的热应力,即使孔铜足够也会有被拉开、拉裂的风险。所以,为了减少这种风险,适当增加孔铜厚度、优化喷锡条件,才能避免风险发生。
四.如何预防孔破与其管制点
1基材
a.CTE造成的孔破,主要应考虑其板材本身的CTE是否能经受住无铅制程的考验;再者就是孔铜厚度管制以现在的无铅焊接而言,IPC所界定的铜厚标准只能满足基本的电性导通,而无法抗击回焊过程中强大的热量冲击,故对于铜厚之管制,建议最低点800 MICRO INCH。
b.针对不同的板材,如:陶瓷、Teflon等,要评估走两次除胶或采用其它方法来满足良好的孔壁金属化。
2钻孔
a.集尘吸力太小,会使得粉屑吸不走,从而造成塞孔。故集尘吸力的大小需设定标准并每班点检,另外就是进、回刀速的设定要结合钻机厂商的建议条件并进行验证再规范化。
b.钻针的使用及寿命管制是非常重要的,因钻针的寿命会影响到孔壁粗糙度,孔限越大,孔壁粗糙度偏大的机率越高,故孔限的设定应以粗糙度不超过1000 MICRO INCH为原则,要勤磨,所谓磨刀不误砍柴工。
c.另外就是对钻针的检验,无论来料还是翻磨要设置专检人员进行抽查监控,防止不良钻针流入 生产线。
d.偏位孔破是因铝片皱褶或是板面有赃物,使得钻针在接触板面时发生偏移,形成偏位孔破。故开料后板面 要清洗干净,同时有皱褶之铝片要禁止使用。
3电镀
1.防止PTH孔破从以下几点管制(所涉参数仅供参考):
a.震动的振幅须管控在0.2-0.4mm;
b.气动的幅度应管控在0.25cm左右(飞靶瞬间上升及下降装置);
c.超声波的电流需管控在3A以上;
d.摇摆幅度有高速、中速、低速三种,应根据实际情况选择,一般摆幅控制在5-7cm;
e.纵横比超过6:1要考虑隔 空插架;
f.高附加值及高纵横比的产品在沉铜时要考虑夹点式挂镀,改变传统的挂篮式沉铜。
g.沉铜线药水严格管制,且各关键药水应配备自动加药系统,以维持药液稳定。
h.每班对沉铜线各生产参数进行点检同时对各辅助装置进行确认,有任何异常及时上报处理。
2.防止镀铜孔破需从以下几点管制:
a.震动的振幅须管控在0.2-0.4mm;
b.摇摆幅度有高速、中速、低速三种,应根据实际情况选择,一般摆幅控制在5-7cm;
c.定时检查夹点螺丝,因缺少会造成铜颗粒进而造成孔塞孔破;
d.至少每年一次对一铜槽液进行活性炭处理,每半年一次对二铜槽液进行活性炭处理;锡槽之四价锡必须定期分析,当四价锡含量≥4g/L时必须作沉降处理。
e.对电镀槽液之添加剂的分析推荐使用CVS分析 ,替代传统的哈氏分析。随着科技的进步,精密仪器对于药液的管理变得举足轻重,化学对于准确性的要求是非常高的。就象医术的发展,各种先进仪器比传统的望闻问切来得更准确。因为电镀药液之有机添加剂的含量均衡对于镀铜延展性的作用是决定性的,虽然有机添加剂含量很小,但其作用却是四两拔升斤,千万不可疏乎大意否则一旦延展性出问题导致孔铜断裂,将可能付出惨重代价。
f.使用高酸低铜的镀铜药水(建议酸铜比为12:1以上),减小镀液粘度,增加分布力及导电性,从而提升镀液的TP值;
g.建议每月一次及重新配槽后对每个镀槽进行延展性测试,这也是对镀液添加剂含量是否稳定及正常的一种辅助验证。通常在新配槽及槽液维护后,槽液中的添加剂含量变化较大,此时极易出现添加剂含量偏低或偏高,故需特别小心。
3.防止锡铅孔破从以下几点管制:
a.震动的振幅需管控在0.2-0.4mm;
b.摇摆幅度有高速、中速、低速三种,应根据实际情况选择,一般摆幅控制在5-7cm;
c.定期分析(建议一周一次)镀液中的四价锡含量,防止因四价锡过高造成镀锡不良。
d.每周两次哈氏试验定性分析光泽剂含量,并适时调整,遗憾的是镀锡光泽剂目前尚无仪器可分析,也缺少方法,故比较直接方法只能是哈氏分析了。
e.按频率测量镀锡厚度,确保厚度正常,提高抗蚀性(200—400 MICRO INCH)
4干膜
a.Tenting孔破,首先应管制在设计上,必须保证最小孔环在4MIL以上,否则不要考虑走TENTING流程。
b.其次,要想办法减少钻孔飞孔问题,杜绝因单个孔偏导致干膜盖孔不良造成的孔破
c.最后就是作业参数的问题了,管制各项参数在标准范围内。
5防焊塞孔
a.防焊塞孔效果的好坏关系到后工序表面处理药水渗入的问题,故不要把塞孔作业当作是应对客户不准透白光,透绿光之规范要求,它实在是防止药水渗入孔内的一道屏障。但塞孔要讲究方法,最保险的作法当然首推三机作业,且用铝片塞孔,并保证塞孔饱满度必须在75%以上,同时孔中间不可有空洞,否则后烤后若绿油出现裂缝,则药水必渗无疑。故针对塞孔要定频率进行切片确认,不可有丝毫马虎。若想提升效率,节省机台而采用二机作业的连塞带印,则一定要验证塞孔饱满度,达不到75%的起码要求,就不根采用二机作业。
b.关于塞孔问题,我们不得佩服日本人的高明,日系客户产品很多导通孔设计为不塞孔,不塞孔则孔内残留药水的机会很小。若绿油工序作业难度导致孔内入油,他们也不允许孔内积墨,但可以允许垂流入孔(即孔壁允许沾油墨,而整个孔则必须是通透的),其最大顾虑依然是担心后工序药水渗入。
6. OSP/化银/化金
a.OSP重工首先要确认好其重工流程,其次管制重工的次数(建议重工次数不要超过两次)
b.在OSP,化银,化金之前处理阶段重点管制微蚀量,不要超出SOP设定值,另外就是若生产过程中出现卡板问题,一定要确认好微蚀段的板子,锁定所有嫌疑板,一旦有孔破迹象,就不要冒险出货,直接打报废处理。
7喷锡
a.热应力是无法消除的,只能选择正确的CTE板材来避免。再者是喷锡温度的管控,要按频率实际测量锡池的温度不要超过上限。
五.总结
总而言之,无论如何管制孔破,不外乎人,机,料,法,环这4M1E,从材料选择,到电镀方法,参数,辅助装置,再到塞孔饱满度,到无铅工序及SMT IR PROFILE各个环节都要严阵以待,真正做到精细管理。PCB在当下已是微利时代,管理上稍有不慎企业盈利就会被赔款蚕食殆尽。
减少孔破不仅是对客户负责,更是对自己负责。我们不奢望能完全杜绝孔破,但改善是无止境的,没有最好,只有更好。管理上有一句话“追根究底,止于至善”,这是我们所有经理人希望到达的境界。